Introduction
In the ever-evolving landscape of the Canadian workplace, the commitment to safety goes beyond mere compliance—it embraces a culture of continuous training and improvement. This blog explores the dynamic strategies employed to foster an environment where safety is not just a checkbox but an ongoing journey of enhancement. From embracing technological advancements to adapting to regulatory changes, with a focal point on the Workplace Hazardous Materials Information System (WHMIS), we delve into the intricate web of continuous training and improvement that defines a safety-centric workplace.
Overview of Workplace Safety Standards
1. Legislative Framework
Workplace safety in Canada is governed by a robust legislative framework aimed at safeguarding employees and ensuring compliance across industries. Federal and provincial regulations collectively shape the foundation for safety standards.
Within this framework, the Workplace Hazardous Materials Information System (WHMIS) plays a pivotal role in setting standards for the safe handling, storage, and disposal of hazardous materials. Employers are mandated to adhere to WHMIS requirements to ensure a secure work environment.
Within this framework, the Workplace Hazardous Materials Information System (WHMIS) plays a pivotal role in setting standards for the safe handling, storage, and disposal of hazardous materials. Employers are mandated to adhere to WHMIS requirements to ensure a secure work environment.
2. Regulatory Authorities
Authorities at the federal and provincial levels oversee the implementation of workplace safety standards. These bodies provide guidelines, conduct inspections, and enforce compliance with established regulations.
Regulatory authorities also actively endorse and enforce WHMIS standards, conducting audits to verify that workplaces adhere to proper labelling, classification, and communication of hazardous materials, reinforcing a culture of safety.
Regulatory authorities also actively endorse and enforce WHMIS standards, conducting audits to verify that workplaces adhere to proper labelling, classification, and communication of hazardous materials, reinforcing a culture of safety.
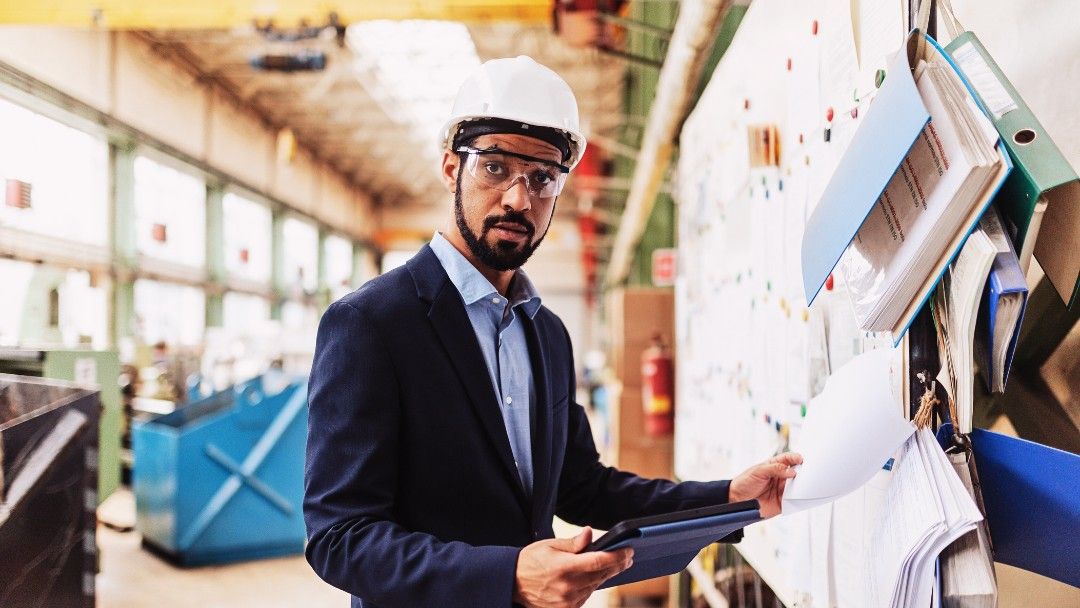
3. Hazard Identification and Risk Assessment
The process of hazard identification and risk assessment is fundamental to workplace safety. Employers are required to assess potential hazards within their specific work environments and implement measures to mitigate risks.
WHMIS aligns seamlessly with this process by providing a standardized classification system for hazardous materials. Employers utilize WHMIS guidelines to accurately identify and assess risks associated with these materials, fostering a proactive approach to safety.
WHMIS aligns seamlessly with this process by providing a standardized classification system for hazardous materials. Employers utilize WHMIS guidelines to accurately identify and assess risks associated with these materials, fostering a proactive approach to safety.
4. Employee Training Programs
Workplace safety standards necessitate comprehensive training programs for employees. Training encompasses various aspects, including emergency procedures, safe work practices, and awareness of potential hazards.
WHMIS training stands as a cornerstone within broader safety programs. It equips employees with the knowledge and skills required to handle hazardous materials safely, promoting a culture of awareness and responsibility in the workplace.
WHMIS training stands as a cornerstone within broader safety programs. It equips employees with the knowledge and skills required to handle hazardous materials safely, promoting a culture of awareness and responsibility in the workplace.
5. Emergency Response Protocols
Workplace safety standards emphasize the importance of having robust emergency response protocols in place. These protocols outline procedures for responding to accidents, incidents, or the release of hazardous materials.
WHMIS contributes to emergency response by ensuring that employees are adequately trained to handle hazardous material incidents. This includes knowledge of proper containment, cleanup, and communication procedures, enhancing overall emergency preparedness.
WHMIS contributes to emergency response by ensuring that employees are adequately trained to handle hazardous material incidents. This includes knowledge of proper containment, cleanup, and communication procedures, enhancing overall emergency preparedness.
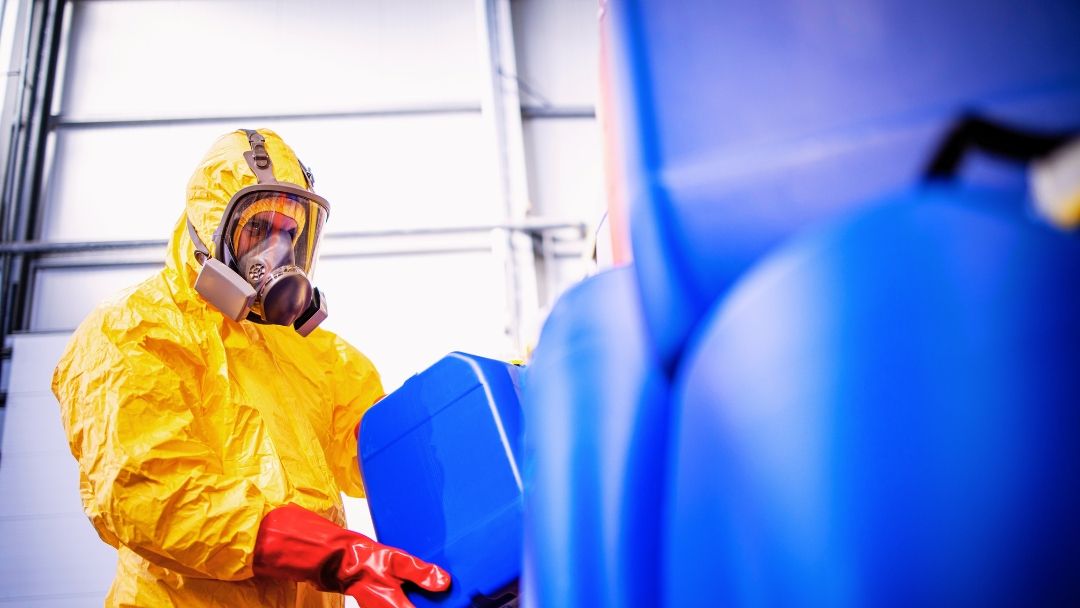
In essence, workplace safety standards in Canada encompass a comprehensive legislative framework, regulatory oversight, hazard identification, employee training, and emergency response protocols. The integration of WHMIS within these standards reinforces a commitment to the safe handling of hazardous materials, ensuring a secure and compliant work environment.
Essential Safety Protocols for Canadian Workplaces
1. Industry-Specific Risk Assessments
Safety protocols in Canadian workplaces begin with comprehensive risk assessments tailored to the specific hazards inherent in each sector. This proactive approach ensures that potential risks are identified and addressed effectively.
Within industry-specific risk assessments, WHMIS is crucial for identifying and mitigating hazards related to hazardous materials. Proper classification, labeling, and communication of these materials are integral components of industry-specific safety protocols.
Within industry-specific risk assessments, WHMIS is crucial for identifying and mitigating hazards related to hazardous materials. Proper classification, labeling, and communication of these materials are integral components of industry-specific safety protocols.
2. Personal Protective Equipment (PPE) Guidelines
Industries in Canada adhere to stringent guidelines regarding the use of Personal Protective Equipment (PPE). These guidelines ensure that employees are equipped with the necessary gear to mitigate risks associated with their specific work environments.
WHMIS contributes to PPE guidelines by providing information on the types of hazardous materials present, guiding the selection of appropriate PPE. This integration enhances the effectiveness of safety protocols tailored to the unique challenges of each industry.
WHMIS contributes to PPE guidelines by providing information on the types of hazardous materials present, guiding the selection of appropriate PPE. This integration enhances the effectiveness of safety protocols tailored to the unique challenges of each industry.
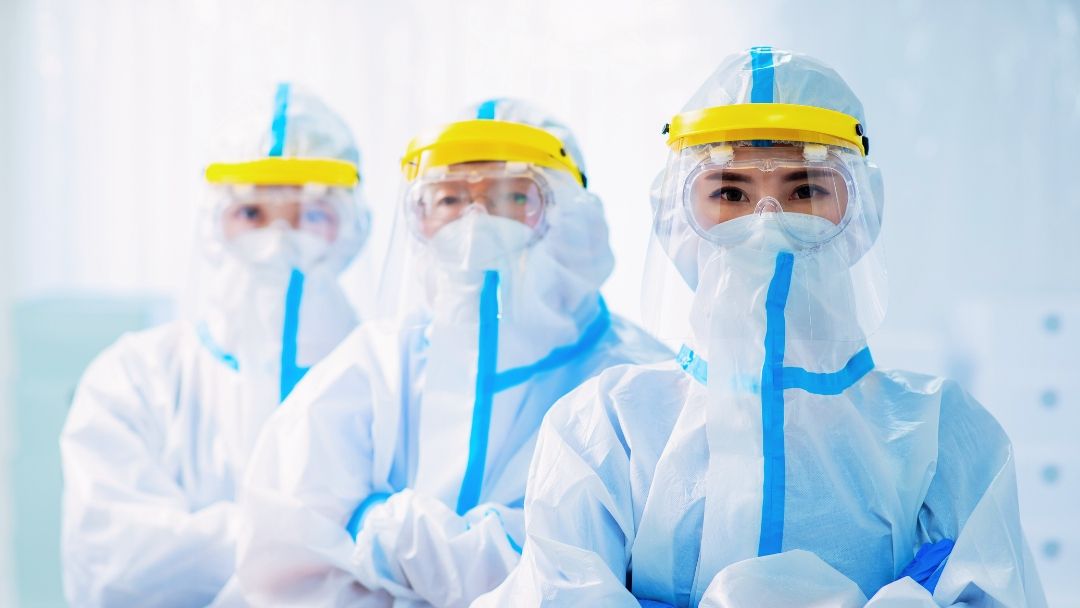
3. Emergency Response Planning
Robust emergency response plans are essential for industries to address unforeseen incidents effectively. These plans outline procedures for evacuation, first aid, and communication during emergencies.
WHMIS aligns with emergency response planning by offering specific guidance on responding to incidents involving hazardous materials. Employees trained in WHMIS protocols play a vital role in executing emergency response plans related to hazardous material incidents.
WHMIS aligns with emergency response planning by offering specific guidance on responding to incidents involving hazardous materials. Employees trained in WHMIS protocols play a vital role in executing emergency response plans related to hazardous material incidents.
4. Equipment Operation and Maintenance Guidelines
Each industry has specific protocols for the operation and maintenance of equipment to ensure both employee safety and the integrity of the workplace. Regular inspections and adherence to guidelines are critical components.
WHMIS contributes to equipment safety by providing information on hazardous materials that may be encountered during equipment operation. This knowledge is integrated into guidelines to ensure safe handling and maintenance practices.
WHMIS contributes to equipment safety by providing information on hazardous materials that may be encountered during equipment operation. This knowledge is integrated into guidelines to ensure safe handling and maintenance practices.
5. Transportation Safety Standards
Industries involved in transportation adhere to stringent safety standards to minimize risks associated with the movement of goods. These standards cover aspects such as vehicle maintenance, driver training, and cargo handling.
WHMIS plays a role in transportation safety by providing information on hazardous materials transported. Employees involved in transportation must undergo WHMIS training to handle, label, and transport hazardous materials safely.
WHMIS plays a role in transportation safety by providing information on hazardous materials transported. Employees involved in transportation must undergo WHMIS training to handle, label, and transport hazardous materials safely.
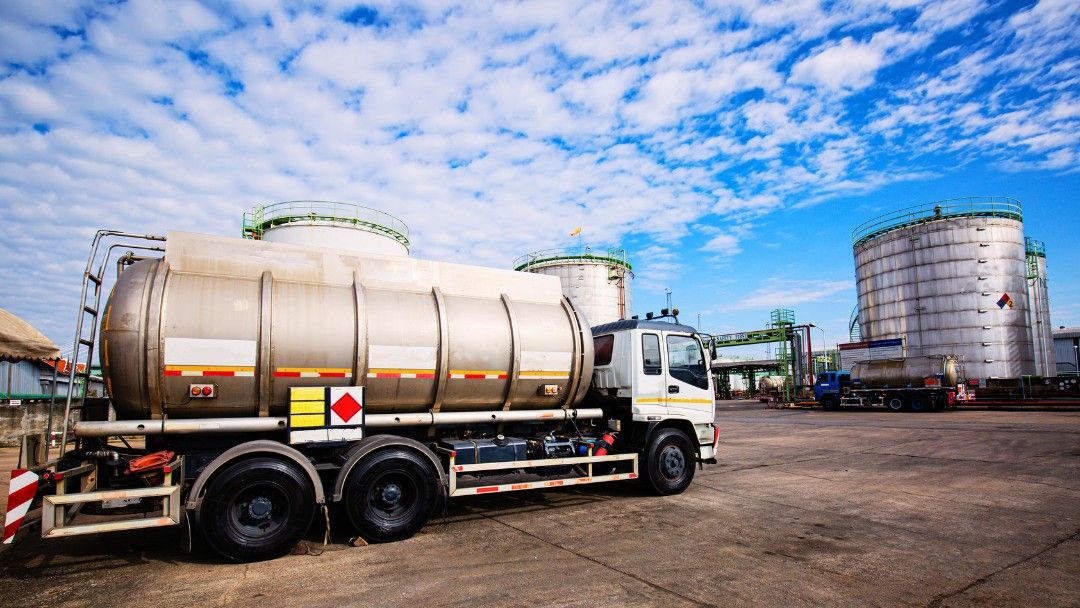
In summary, essential safety protocols for various industries in Canada encompass industry-specific risk assessments, PPE guidelines, emergency response planning, equipment operation and maintenance, and transportation safety standards. The integration of WHMIS within these protocols ensures that industries address the unique challenges posed by hazardous materials, fostering a culture of safety and compliance.
Emergency Preparedness and Response
1. Comprehensive Emergency Preparedness Plans
The foundation of emergency preparedness lies in the development of comprehensive plans tailored to the specific risks of each workplace. These plans encompass procedures for evacuation, first aid, and communication during emergency situations.
WHMIS contributes to emergency preparedness by addressing the unique challenges associated with hazardous materials. It ensures that emergency plans include specific protocols for incidents involving the release, exposure, or spill of hazardous materials.
WHMIS contributes to emergency preparedness by addressing the unique challenges associated with hazardous materials. It ensures that emergency plans include specific protocols for incidents involving the release, exposure, or spill of hazardous materials.
2. Employee Training and Drills
Ensuring that employees are well-trained for emergency situations is paramount. Regular drills and training sessions familiarize employees with emergency procedures, enhancing their preparedness and response capabilities.
WHMIS training is an integral component of employee preparedness. Employees who have completed WHMIS training are educated on the identification and handling of hazardous materials, enabling them to respond effectively in situations involving these materials.
WHMIS training is an integral component of employee preparedness. Employees who have completed WHMIS training are educated on the identification and handling of hazardous materials, enabling them to respond effectively in situations involving these materials.
3. Communication Protocols
Clear communication is critical during emergencies. Protocols for effective communication, both internal and external, are established to relay crucial information to employees, emergency responders, and relevant authorities.
WHMIS contributes to communication protocols by emphasizing standardized labelling and communication of hazardous materials. This ensures that information about the nature of materials involved is conveyed swiftly and accurately during emergencies.
WHMIS contributes to communication protocols by emphasizing standardized labelling and communication of hazardous materials. This ensures that information about the nature of materials involved is conveyed swiftly and accurately during emergencies.
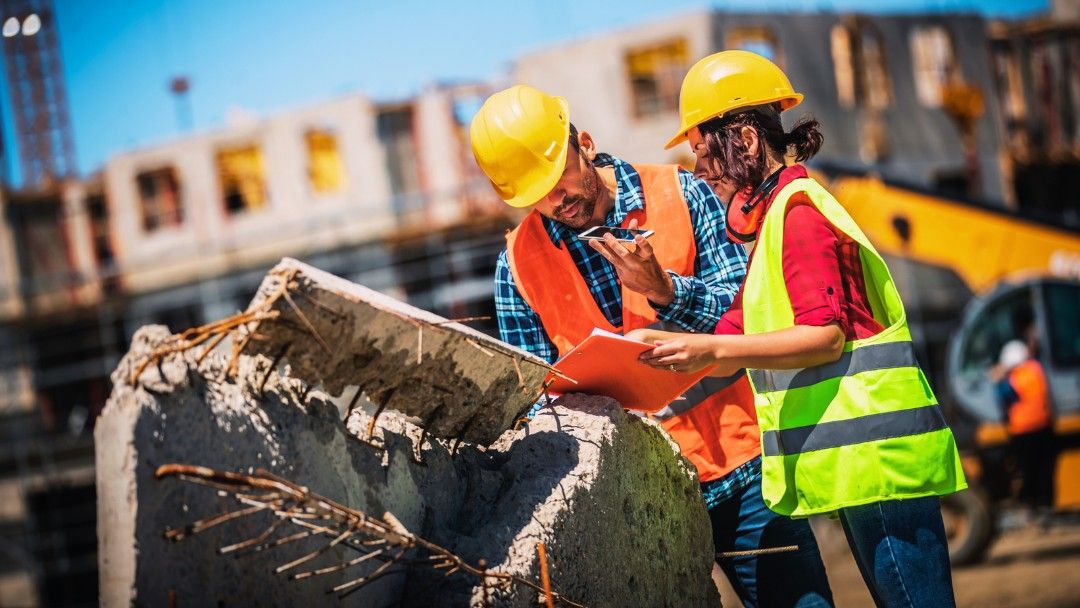
4. Hazardous Material Containment and Cleanup
Emergency response plans include specific protocols for containing and cleaning up hazardous materials to prevent further harm to individuals and the environment. These protocols adhere to regulatory standards.
WHMIS plays a crucial role in the containment and cleanup of hazardous materials by providing information on proper handling and disposal procedures. Emergency responders trained in WHMIS can address incidents involving hazardous materials effectively.
WHMIS plays a crucial role in the containment and cleanup of hazardous materials by providing information on proper handling and disposal procedures. Emergency responders trained in WHMIS can address incidents involving hazardous materials effectively.
5. Coordination with Emergency Services
Establishing coordination with local emergency services is vital for a prompt and effective response. Emergency services are integrated into the planning process, and communication channels are established for seamless collaboration.
WHMIS training aligns with emergency services coordination by ensuring that responders are familiar with the hazardous materials involved. This knowledge facilitates collaborative efforts in containing and resolving incidents.
WHMIS training aligns with emergency services coordination by ensuring that responders are familiar with the hazardous materials involved. This knowledge facilitates collaborative efforts in containing and resolving incidents.
Emergency preparedness and response in the Canadian workplace encompasses comprehensive plans, employee training, communication protocols, hazardous material containment, and coordination with emergency services. The integration of WHMIS within these aspects ensures a specialized and effective response to incidents involving hazardous materials, contributing to overall workplace safety and compliance.
Continuous Training and Improvement in Workplace Safety
1. Ongoing Employee Training Programs
OA commitment to workplace safety involves the establishment of continuous training programs. These programs ensure that employees stay abreast of evolving safety standards, protocols, and industry best practices.
Within the realm of continuous training, WHMIS stands as a cornerstone. Regular updates on WHMIS regulations and procedures need to be provided to employees, enhancing their knowledge and skills in handling hazardous materials safely.
Within the realm of continuous training, WHMIS stands as a cornerstone. Regular updates on WHMIS regulations and procedures need to be provided to employees, enhancing their knowledge and skills in handling hazardous materials safely.
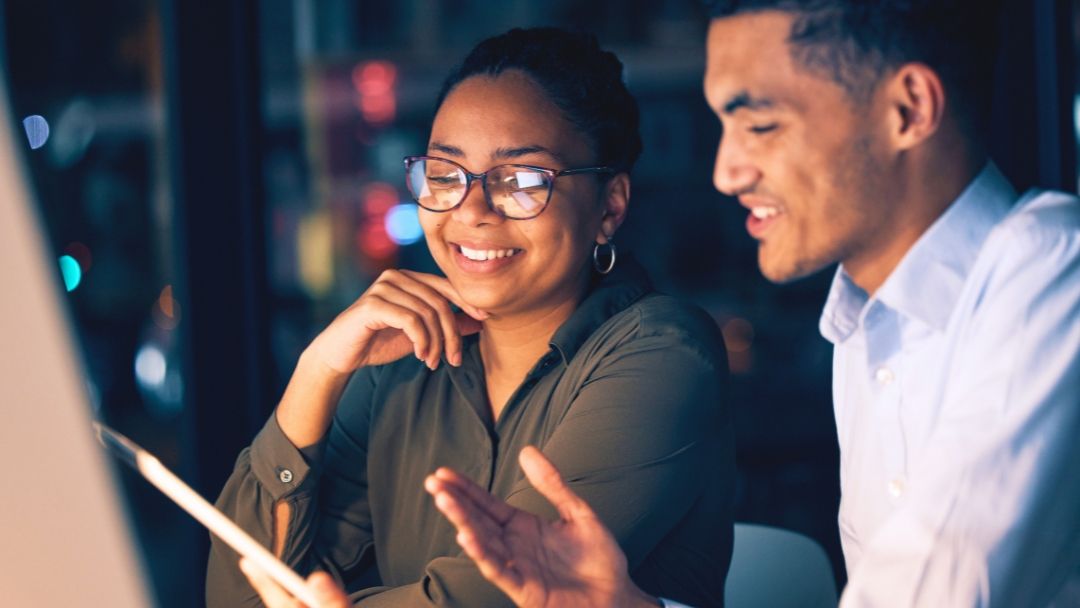
2. Adapting to Regulatory Changes
Workplace safety is dynamic, with regulatory changes being a constant factor. Continuous improvement involves adapting to these changes and ensuring that safety protocols align with the latest regulatory requirements.
WHMIS facilitates continuous improvement by incorporating changes in hazardous material regulations. Employees should be trained on updated WHMIS standards, ensuring compliance with the latest legal requirements.
WHMIS facilitates continuous improvement by incorporating changes in hazardous material regulations. Employees should be trained on updated WHMIS standards, ensuring compliance with the latest legal requirements.
3. Regular Safety Audits and Inspections
Conducting regular safety audits and inspections is crucial for identifying potential hazards and assessing the effectiveness of safety protocols. These audits provide insights into areas that require improvement.
WHMIS aligns with safety audits by focusing on the proper classification, labeling, and communication of hazardous materials. Audits specifically assess compliance with WHMIS standards, ensuring adherence to safety protocols.
WHMIS aligns with safety audits by focusing on the proper classification, labeling, and communication of hazardous materials. Audits specifically assess compliance with WHMIS standards, ensuring adherence to safety protocols.
4. Employee Feedback Mechanisms
Establishing mechanisms for employee feedback encourages active participation in the improvement process. Employees' insights and observations contribute to identifying areas for enhancement.
WHMIS training programs benefit from employee feedback. Employees can provide input on the effectiveness of WHMIS training modules, ensuring that the content remains relevant and impactful.
WHMIS training programs benefit from employee feedback. Employees can provide input on the effectiveness of WHMIS training modules, ensuring that the content remains relevant and impactful.
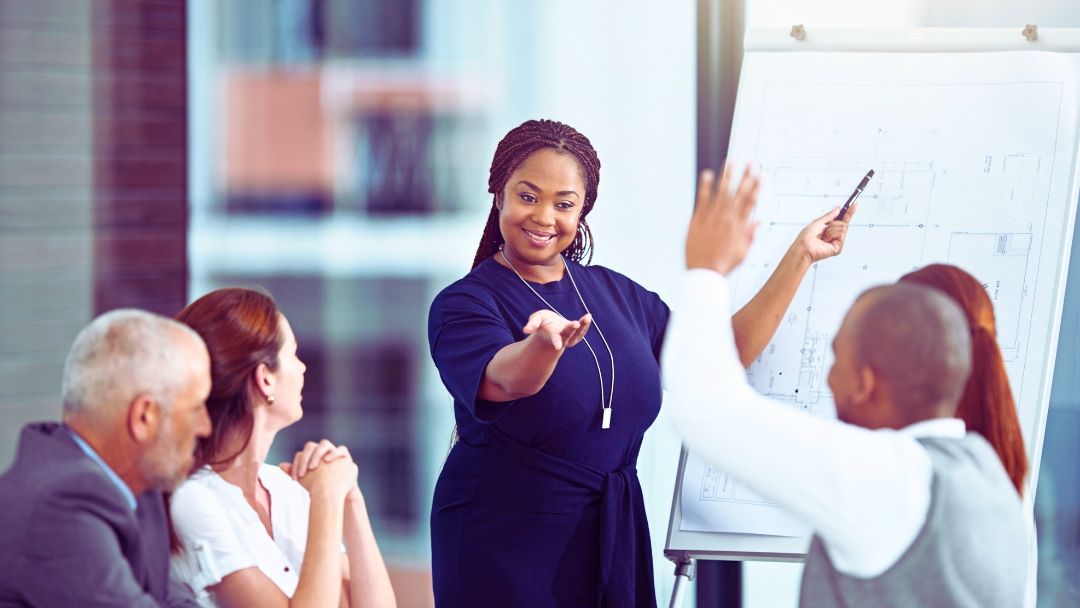
5. Technological Integration in Training
Embracing technology in training initiatives enhances accessibility and engagement. Interactive online modules, webinars, and e-learning platforms are employed to deliver training, allowing employees to learn at their own pace.
Our WHMIS training leverages technology by incorporating online modules and an interactive platform. This approach ensures that employees receive engaging and up-to-date training on hazardous materials and safety procedures.
Our WHMIS training leverages technology by incorporating online modules and an interactive platform. This approach ensures that employees receive engaging and up-to-date training on hazardous materials and safety procedures.
6. Industry-Specific Learning Resources
Continuous improvement is most effective when it aligns with industry-specific needs. Providing access to industry-specific learning resources ensures that employees acquire knowledge directly applicable to their roles.
WHMIS contributes to industry-specific learning by tailoring training to the hazards present in specific industries. Through WHMIS training, employees gain insights into the unique challenges associated with handling hazardous materials in their respective workplaces.
WHMIS contributes to industry-specific learning by tailoring training to the hazards present in specific industries. Through WHMIS training, employees gain insights into the unique challenges associated with handling hazardous materials in their respective workplaces.
7. Incentives for Continued Learning
Recognizing and incentivizing employees who actively engage in continuous learning is a motivating factor. Rewards, certificates, or other incentives can drive a culture of ongoing development.
Incentives for continued learning are extended to employees participating in WHMIS training. Recognizing their commitment to mastering the safe handling of hazardous materials reinforces a safety-oriented culture.
Incentives for continued learning are extended to employees participating in WHMIS training. Recognizing their commitment to mastering the safe handling of hazardous materials reinforces a safety-oriented culture.
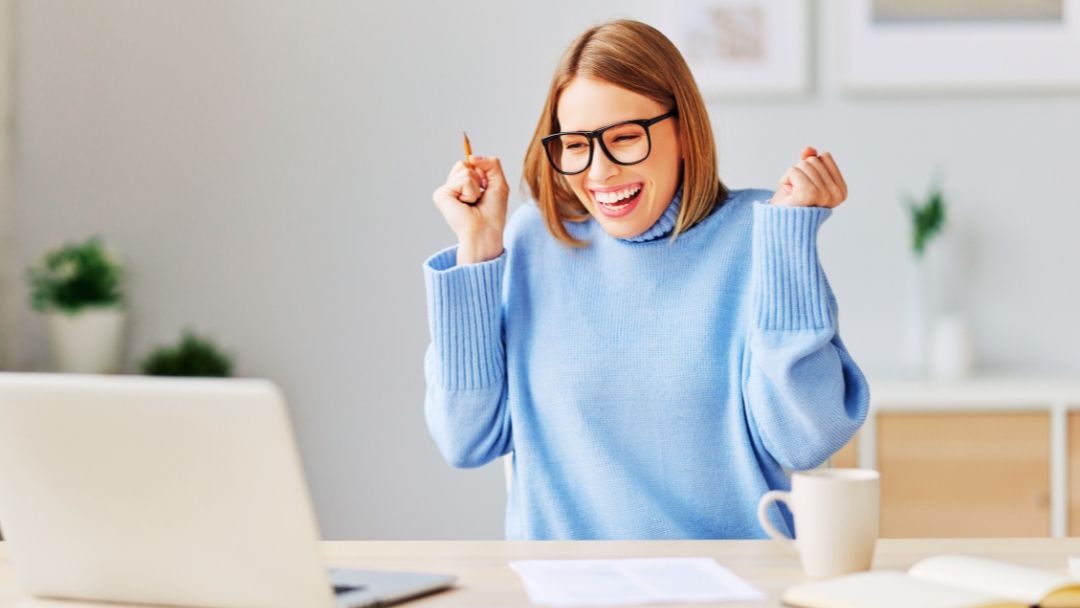
Continuous training and improvement in workplace safety involve ongoing employee training, adaptation to regulatory changes, safety audits, employee feedback mechanisms, technological integration, industry-specific resources, and incentives for continued learning. The integration of WHMIS ensures that employees are equipped with the latest knowledge and skills related to hazardous materials, fostering a workplace committed to continual safety enhancement.
Conclusion
As we conclude our exploration into continuous training and improvement in workplace safety, one resounding truth emerges: safety is a journey, not a destination. The commitment to ongoing employee training, adaptation to regulatory shifts, regular safety audits, and the integration of feedback mechanisms create a robust framework. Technological innovations, industry-specific resources, and incentives for continued learning propel this journey forward.
With WHMIS as a guiding force, employees are equipped not just with knowledge but with a mindset that prioritizes safety at every turn. Together, these elements weave a tapestry of workplace safety that is not only compliant but continually evolving—a testament to an unwavering commitment to the well-being of every individual in the workplace.
With WHMIS as a guiding force, employees are equipped not just with knowledge but with a mindset that prioritizes safety at every turn. Together, these elements weave a tapestry of workplace safety that is not only compliant but continually evolving—a testament to an unwavering commitment to the well-being of every individual in the workplace.
Level up your workplace safety!