Introduction
In the ever-evolving landscape of workplace safety, the significance of WHMIS (Workplace Hazardous Materials Information System) certification cannot be overstated. As industries diversify and encounter a myriad of hazardous materials, the need for comprehensive training tailored to specific sectors becomes paramount.
This blog delves into the intricate realm of "Industry-Specific Considerations for WHMIS Certification," exploring how this crucial certification adapts to the nuances of different workplaces. From tailoring training to industry hazards to recognizing industry-specific symbols, each facet contributes to the overarching goal of fostering a culture of safety and compliance.
Join us on a journey through the intricacies of WHMIS certification, where the safety of employees takes center stage, irrespective of the industry they serve.
This blog delves into the intricate realm of "Industry-Specific Considerations for WHMIS Certification," exploring how this crucial certification adapts to the nuances of different workplaces. From tailoring training to industry hazards to recognizing industry-specific symbols, each facet contributes to the overarching goal of fostering a culture of safety and compliance.
Join us on a journey through the intricacies of WHMIS certification, where the safety of employees takes center stage, irrespective of the industry they serve.
Understanding the Importance of WHMIS Certification
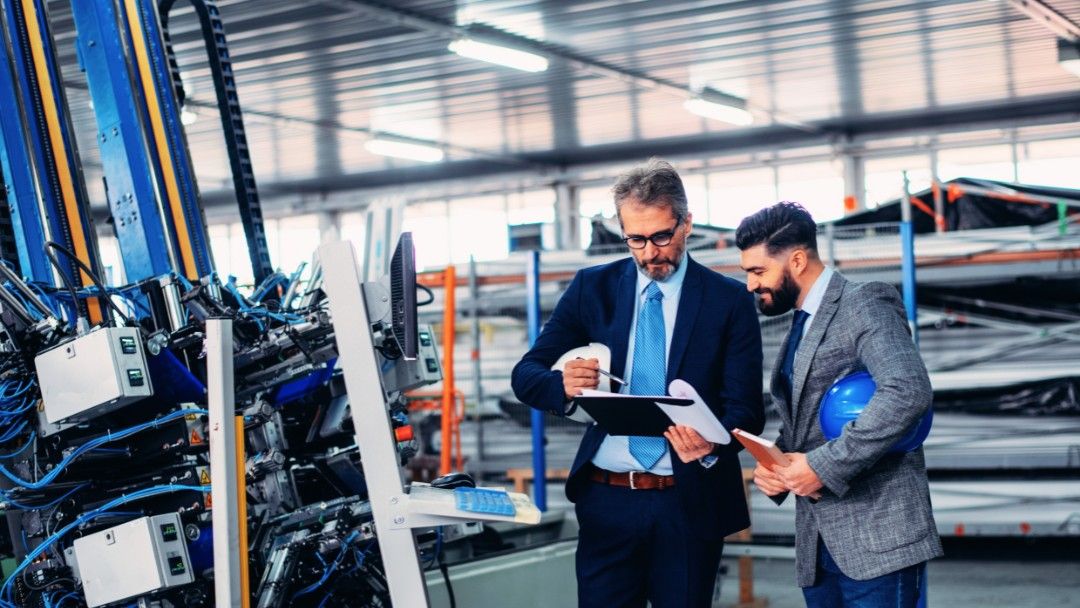
1. Legal Compliance and Regulatory Adherence
WHMIS certification is a legal requirement in Canada, ensuring that workplaces comply with federal and provincial regulations related to the safe handling, storage, and disposal of hazardous materials.
For example, in a manufacturing facility, employees undergo WHMIS certification to adhere to legal standards. This includes understanding the proper labelling of chemical containers, knowing the potential hazards, and following the established protocols for handling these materials.
For example, in a manufacturing facility, employees undergo WHMIS certification to adhere to legal standards. This includes understanding the proper labelling of chemical containers, knowing the potential hazards, and following the established protocols for handling these materials.
2. Employee Safety and Hazard Awareness
WHMIS certification plays a crucial role in enhancing employee safety by raising awareness about potential workplace hazards. It empowers employees to identify and respond to hazardous materials appropriately.
As an example, in a laboratory setting, WHMIS-certified researchers are equipped to recognize the symbols on chemical labels, understand Safety Data Sheets (SDSs), and take necessary precautions to prevent accidents or exposure to harmful substances.
As an example, in a laboratory setting, WHMIS-certified researchers are equipped to recognize the symbols on chemical labels, understand Safety Data Sheets (SDSs), and take necessary precautions to prevent accidents or exposure to harmful substances.
3. Emergency Preparedness and Response
WHMIS certification includes training on emergency response procedures, ensuring that employees are well-prepared to handle incidents involving hazardous materials.
In construction sites, for example, WHMIS-certified workers are trained to respond effectively in case of a chemical spill. They know the designated emergency exits, the location of emergency equipment, and the steps to take to minimize risks during such situations.
In construction sites, for example, WHMIS-certified workers are trained to respond effectively in case of a chemical spill. They know the designated emergency exits, the location of emergency equipment, and the steps to take to minimize risks during such situations.
4. Safe Handling and Storage Practices
WHMIS certification imparts knowledge on the safe handling, storage, and disposal of hazardous materials, reducing the risk of accidents and ensuring a secure work environment.
In the setting of a warehouse storing chemical products, WHMIS-certified employees would understand the compatibility of different substances, use proper storage containers, and follow established protocols to minimize the risk of spills or leaks.
In the setting of a warehouse storing chemical products, WHMIS-certified employees would understand the compatibility of different substances, use proper storage containers, and follow established protocols to minimize the risk of spills or leaks.
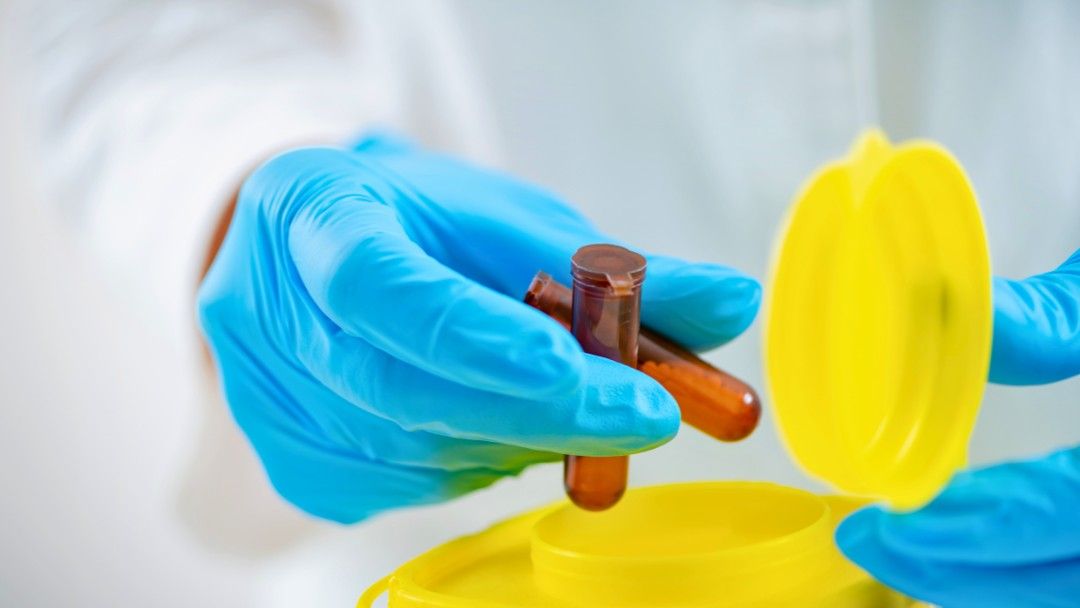
5. Communication and Collaboration
WHMIS certification fosters effective communication about hazardous materials within the workplace, promoting collaboration among employees to maintain a safe and informed environment.
For example, in an office setting, WHMIS-certified employees communicate chemical hazards to cleaning staff. They ensure that cleaning products used in common areas are clearly labelled, and information is shared to prevent any adverse reactions or mishandling.
For example, in an office setting, WHMIS-certified employees communicate chemical hazards to cleaning staff. They ensure that cleaning products used in common areas are clearly labelled, and information is shared to prevent any adverse reactions or mishandling.
6. Continuous Learning and Updates
WHMIS certification requires periodic renewal, encouraging continuous learning and keeping employees informed about evolving safety standards and regulations.
In research and development facilities, WHMIS-certified scientists should undergo regular updates to stay informed about changes in chemical classifications. This ensures that they are always aware of the latest safety protocols when working with new materials.
In research and development facilities, WHMIS-certified scientists should undergo regular updates to stay informed about changes in chemical classifications. This ensures that they are always aware of the latest safety protocols when working with new materials.
7. Employer Liability Reduction
WHMIS certification reduces employer liability by demonstrating a commitment to safety and compliance with regulations, potentially minimizing legal risks associated with workplace incidents.
In a manufacturing plant, employers should require workers to complete WHMIS certification. This commitment not only protects employees but also reduces the risk of legal consequences in the event of an accident.
In a manufacturing plant, employers should require workers to complete WHMIS certification. This commitment not only protects employees but also reduces the risk of legal consequences in the event of an accident.
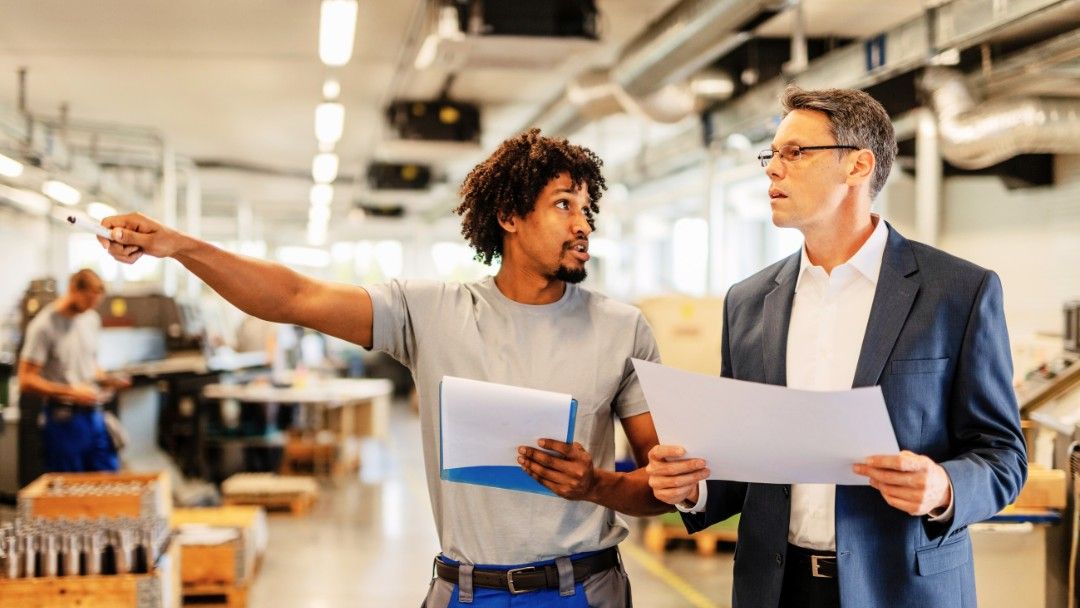
Understanding the importance of WHMIS certification involves legal compliance, employee safety, emergency preparedness, safe handling practices, effective communication, continuous learning, and liability reduction. These examples illustrate how WHMIS certification is integral to creating a workplace that prioritizes safety and mitigates risks associated with hazardous materials.
WHMIS Training Requirements and Duration
1. Mandatory Training for All Employees
WHMIS training is mandatory for all employees who may be exposed to hazardous materials in the workplace. This requirement ensures that everyone, regardless of their role, has a fundamental understanding of potential hazards.
As an example, in a manufacturing plant, all employees - from production workers to office staff - need to undergo WHMIS training. This includes understanding the labelling of chemical containers, recognizing hazard symbols, and knowing emergency response procedures.
As an example, in a manufacturing plant, all employees - from production workers to office staff - need to undergo WHMIS training. This includes understanding the labelling of chemical containers, recognizing hazard symbols, and knowing emergency response procedures.
2. Varied Training Levels Based on Exposure
The level of WHMIS training may vary depending on the degree of exposure to hazardous materials. Different job roles may require different levels of training to address specific workplace risks.
In a laboratory setting, researchers handling potent chemicals should receive advanced WHMIS training, covering in-depth knowledge of Material Safety Data Sheets (MSDS) and specific emergency response protocols. Office employees may undergo a more basic level of training tailored to their lower exposure.
In a laboratory setting, researchers handling potent chemicals should receive advanced WHMIS training, covering in-depth knowledge of Material Safety Data Sheets (MSDS) and specific emergency response protocols. Office employees may undergo a more basic level of training tailored to their lower exposure.
3. Frequency of Training Renewals
WHMIS training requires regular renewals to ensure that employees stay informed about changes in regulations and best practices. This ongoing training promotes continuous learning and updates.
In construction, workers renew their WHMIS training every year. This renewal process includes updates on new hazardous materials, changes in safety protocols, and any modifications in regulatory requirements.
In construction, workers renew their WHMIS training every year. This renewal process includes updates on new hazardous materials, changes in safety protocols, and any modifications in regulatory requirements.
4. Duration and Format of Training Sessions
WHMIS training sessions are structured to cover essential content comprehensively. The duration and format may vary, accommodating the diverse needs of different workplaces.
In a retail environment selling cleaning products, employees may receive concise WHMIS training during onboarding, lasting for an hour. In contrast, employees in a chemical manufacturing facility might undergo more extensive training sessions spanning multiple days.
In a retail environment selling cleaning products, employees may receive concise WHMIS training during onboarding, lasting for an hour. In contrast, employees in a chemical manufacturing facility might undergo more extensive training sessions spanning multiple days.
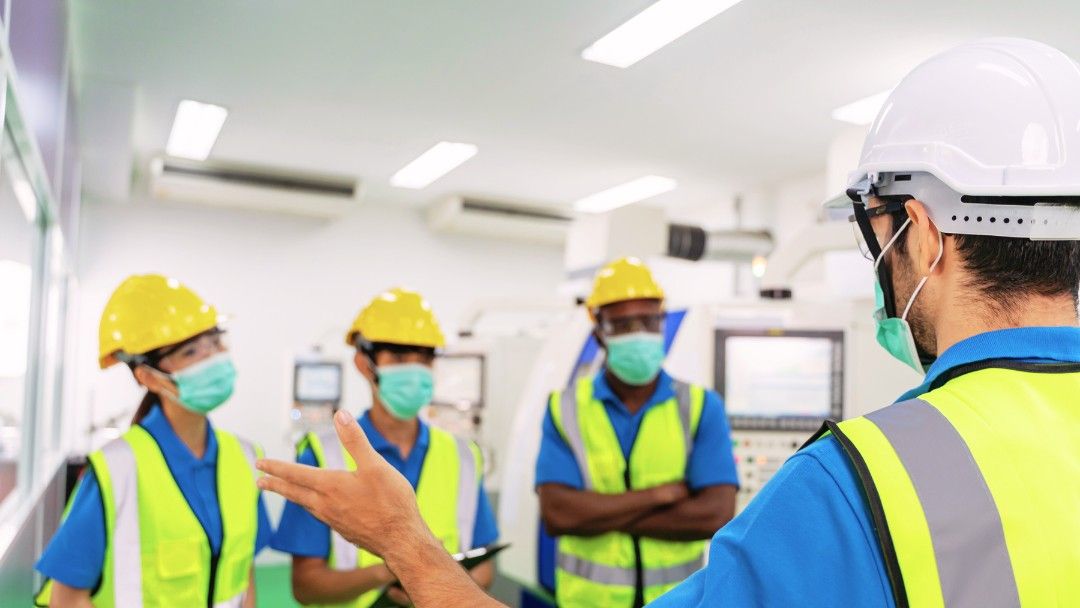
5. Tailoring Training to Specific Industries
WHMIS training can be tailored to specific industries, addressing the unique hazards associated with various sectors. This industry-specific approach ensures that training is relevant to the workplace.
In a healthcare setting, WHMIS training is customized to address the specific hazards of medical substances. Employees learn about the safe handling of pharmaceuticals, potential reactions, and the importance of clear communication regarding patient care products.
In a healthcare setting, WHMIS training is customized to address the specific hazards of medical substances. Employees learn about the safe handling of pharmaceuticals, potential reactions, and the importance of clear communication regarding patient care products.
6. Integration with Overall Health and Safety Programs
WHMIS training is often integrated into broader health and safety programs within organizations. This integration ensures that WHMIS aligns with overall workplace safety initiatives.
In logistics, WHMIS training should be part of a comprehensive health and safety program. Employees learn about the hazards associated with transporting various materials and receive training on proper handling during shipping and delivery processes.
In logistics, WHMIS training should be part of a comprehensive health and safety program. Employees learn about the hazards associated with transporting various materials and receive training on proper handling during shipping and delivery processes.
7. Specialized Training for Designated Individuals
Certain individuals within a workplace may require specialized WHMIS training based on their responsibilities. This targeted training ensures that those handling specific aspects of hazardous materials are well-equipped.
For example, in a chemical research facility, individuals responsible for waste disposal undergo specialized WHMIS training focused on the safe disposal of chemical by-products. This training includes understanding regulatory requirements for waste management.
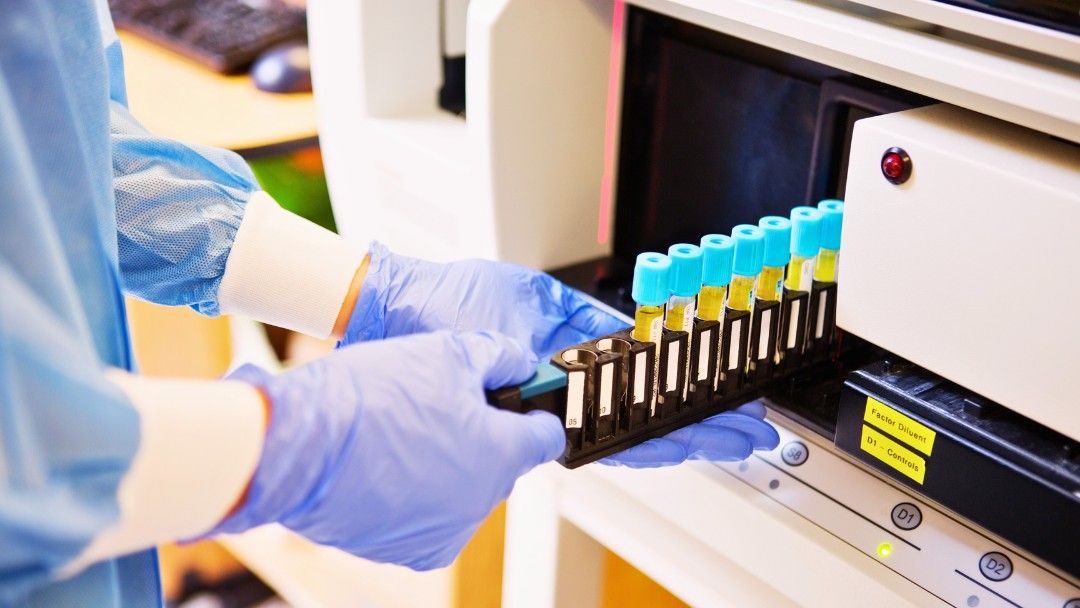
Understanding WHMIS training requirements and duration involves mandatory training for all employees, varied training levels based on exposure, regular training renewals, tailored industry-specific training, integration with overall health and safety programs, and specialized training for designated individuals. These examples illustrate how WHMIS training is designed to be comprehensive, adaptable, and aligned with the specific needs of diverse workplaces.
Obtaining and Renewing WHMIS Certification
1. Initial Certification Process
Obtaining WHMIS certification involves an initial training process to equip employees with the necessary knowledge and skills for handling hazardous materials. This certification is typically a prerequisite for working in environments where exposure to such materials is possible.
New employees at a chemical manufacturing plant would undergo an initial WHMIS certification program during their onboarding process. This program covers the basics of hazard identification, safe handling practices, and emergency response procedures.
2. Ongoing Training for New Employees
Employers must ensure that new employees receive WHMIS certification promptly upon starting their roles. This ensures that all workers - regardless of when they join the organization - are adequately trained to work safely with hazardous materials.
For example, a construction company would conduct regular orientation sessions for new hires, including WHMIS certification. Even employees joining the company mid-year participate in these sessions to maintain a consistently trained workforce.
3. Renewal Requirements and Frequency
WHMIS certification is subject to renewal at regular intervals to keep employees informed about updates in regulations, emerging hazards, and changes in safety protocols. The renewal frequency varies based on regional regulations and industry standards.
In a laboratory setting, employees should renew their WHMIS certification at least every three years. This renewal process includes updates on new research materials, advancements in safety measures, and any modifications in regulatory requirements.
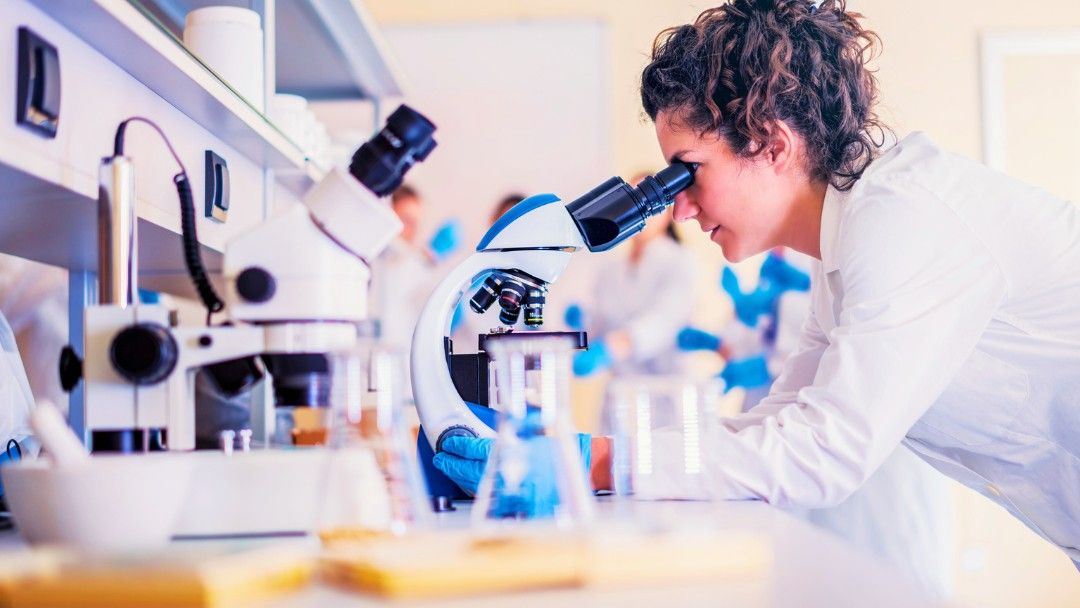
4. Integration with Health and Safety Programs
Renewing WHMIS certification is often integrated into broader health and safety programs within organizations. This integration ensures that WHMIS aligns with overall workplace safety initiatives, creating a holistic approach to employee well-being.
A manufacturing company might integrate WHMIS certification renewal into its annual health and safety training program. Employees participate in refresher courses alongside other safety topics to maintain a comprehensive understanding of workplace risks.
5. Continuous Learning and Skill Development
Renewing WHMIS certification provides an opportunity for continuous learning and skill development. This process reinforces employees' knowledge, updates them on best practices, and enhances their ability to respond effectively to hazardous materials.
In a pharmaceutical research facility, employees engage in continuous learning during WHMIS certification renewals. This includes updates on new chemical compounds, advancements in safety technologies, and practical exercises to reinforce emergency response skills.
6. Customization for Industry-Specific Needs
The renewal process for WHMIS certification can be customized to address industry-specific needs and hazards. This ensures that employees receive targeted training relevant to the materials they encounter in their specific work environments.
For example, employees in a food processing plant may undergo WHMIS certification renewal with a focus on the unique hazards associated with food-grade chemicals. The training would address specific risks related to food production and processing.
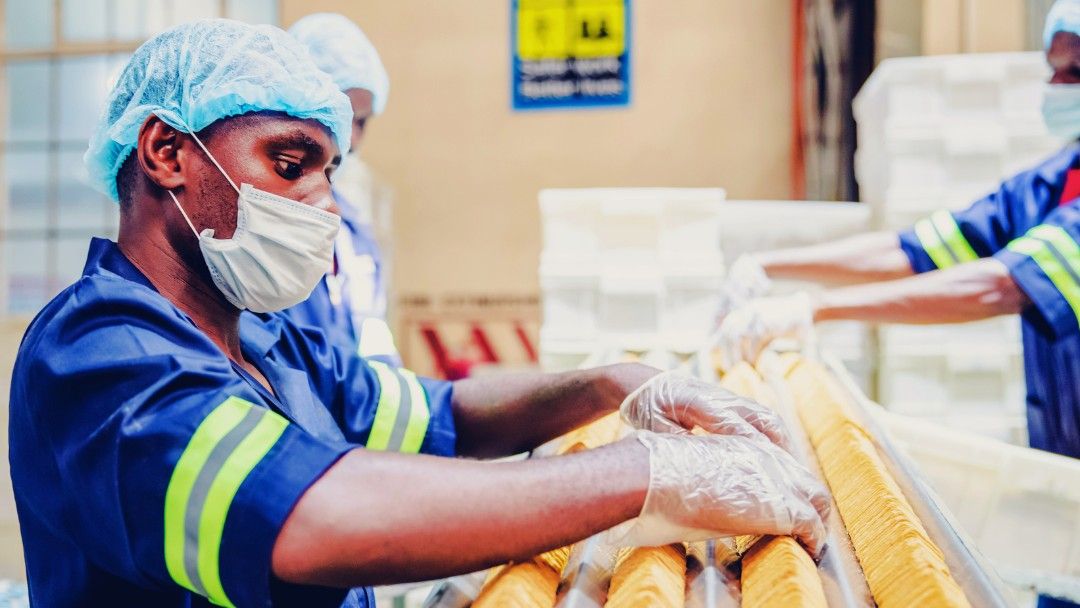
7. Digital Training Platforms and Accessibility
Employers may utilize digital training platforms for WHMIS certification renewal, enhancing accessibility and flexibility for employees. Online modules, webinars, and e-learning platforms provide convenient options for ongoing training.
A specific example of this would be a logistics company that offers employees the option to renew their WHMIS certification through an online platform. This allows employees to complete the renewal process at their own pace, accommodating different schedules and work shifts.
Obtaining and renewing WHMIS certification involves an initial certification process, ongoing training for new employees, renewal requirements and frequency, integration with health and safety programs, continuous learning and skill development, customization for industry-specific needs, and the use of digital training platforms. These examples illustrate how the certification process is designed to be comprehensive, adaptable, and accessible to ensure ongoing workplace safety.
Industry-Specific Considerations for WHMIS Certification
1. Tailoring Training to Industry Hazards
WHMIS certification can be tailored to address specific hazards prevalent in different industries. This approach ensures that employees receive training relevant to the materials and risks unique to their work environments.
In the automotive manufacturing industry, WHMIS certification is customized to focus on hazards associated with chemicals used in painting processes, such as paints, solvents, and coatings.
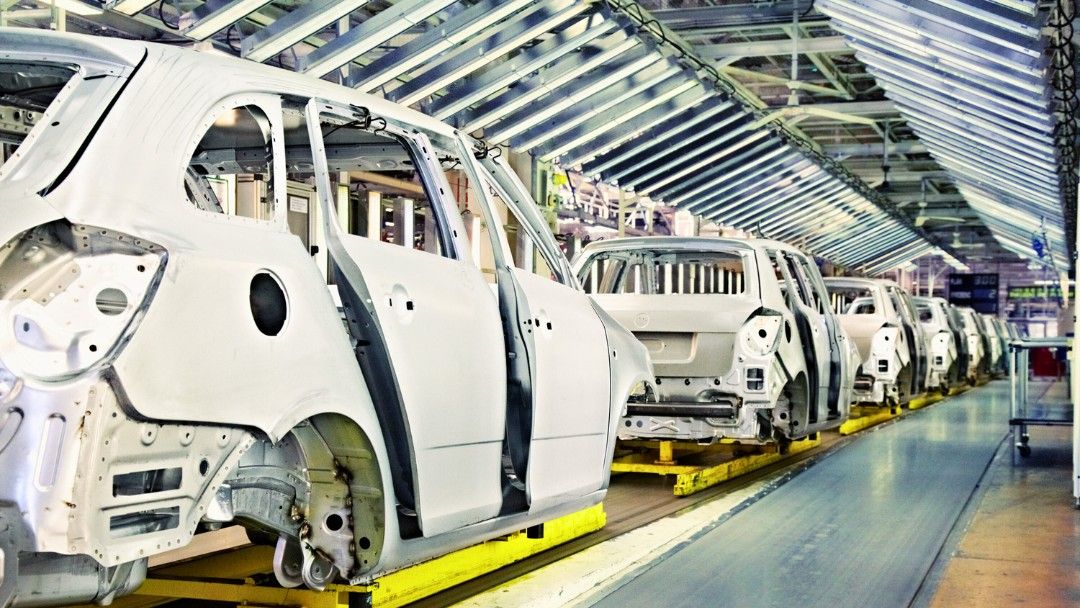
2. Specialized Modules for Unique Materials
Some industries deal with unique hazardous materials that require specialized knowledge. WHMIS certification programs can include specific modules addressing the handling and safety considerations for these materials.
In the agricultural sector, WHMIS certification incorporates specialized modules on the safe use of pesticides, herbicides, and fertilizers, providing targeted guidance for workers in this industry.
3. Compliance with Industry Regulations
Industries often have specific regulations governing the handling of hazardous materials. WHMIS certification programs take into account these industry-specific regulations to ensure compliance.
In the healthcare sector, WHMIS certification aligns with regulations governing the safe handling of pharmaceuticals and medical chemicals, ensuring healthcare professionals adhere to industry-specific guidelines.
4. Consideration of Work Processes
Different industries have distinct work processes that may impact the handling of hazardous materials. WHMIS certification programs consider these processes to provide practical guidance for safe material handling.
In the construction industry, WHMIS certification addresses the unique work processes involved in building construction, including the use of concrete additives, sealants, and adhesives.
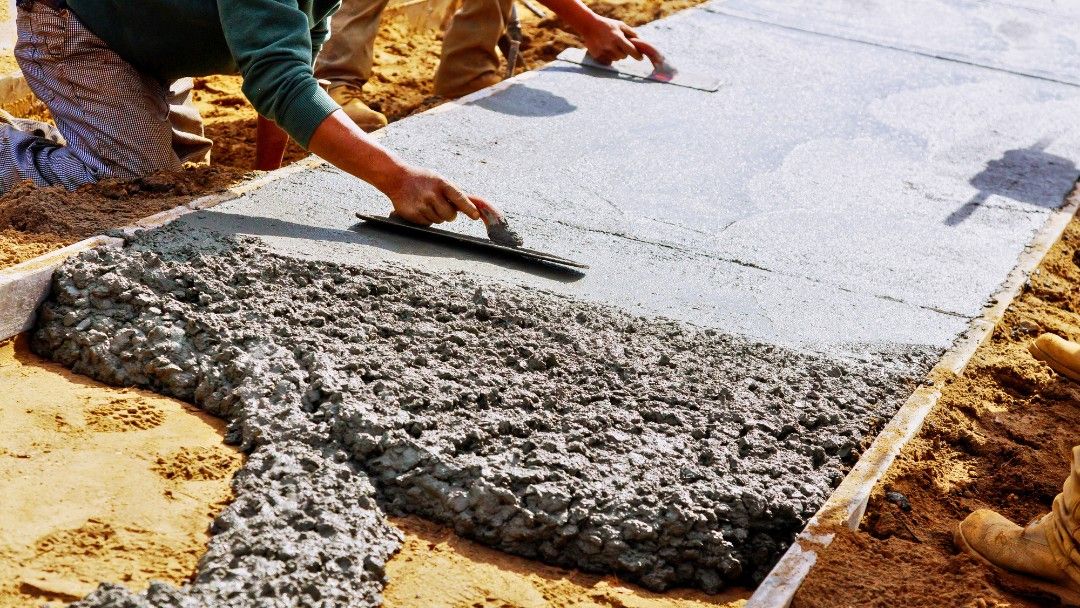
5. Emergency Response Planning Specific to Industry
Emergency response planning as part of WHMIS certification may need to be tailored to address industry-specific scenarios. This ensures that employees are well-prepared for potential emergencies in their particular work environments.
In the petrochemical industry, WHMIS certification includes specific emergency response planning for incidents involving flammable liquids, gases, and other hazardous substances commonly found in this sector.
6. Integration with Industry Training Programs
WHMIS certification is seamlessly integrated with broader industry training programs. This integration ensures that WHMIS aligns with overall industry safety initiatives and contributes to a comprehensive approach to employee well-being.
In the mining industry, WHMIS certification is part of a larger safety training program that covers hazards associated with mining activities, such as exposure to dust, chemicals, and heavy machinery.
7. Recognition of Industry-Specific Symbols and Labels
Different industries may use specific symbols and labels to communicate hazards. WHMIS certification acknowledges and teaches employees to recognize these industry-specific symbols and labels for effective communication.
In the electronics manufacturing industry, WHMIS certification includes training on recognizing industry-specific symbols indicating the presence of hazardous materials used in electronic components.
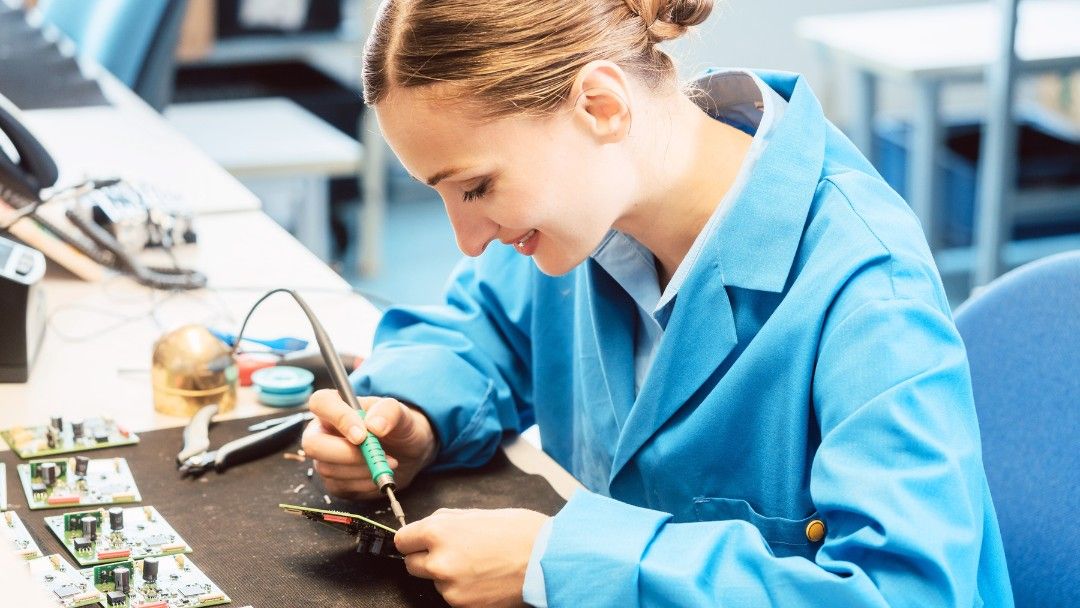
Industry-specific considerations for WHMIS certification involve tailoring training to industry hazards, including specialized modules for unique materials, compliance with industry regulations, consideration of work processes, emergency response planning specific to the industry, integration with industry training programs, and recognition of industry-specific symbols and labels. These examples highlight the adaptability of WHMIS certification to diverse industries, ensuring that training meets the specific needs of each sector.
Conclusion
In the tapestry of workplace safety, WHMIS certification weaves a thread of adaptability and resilience. It transforms from a generic training program into a dynamic tool, catering to the intricate needs of diverse industries.
By tailoring training, recognizing unique materials, ensuring regulatory compliance, considering industry-specific processes, planning for emergencies, integrating with broader training initiatives, and fostering symbol literacy, WHMIS certification stands as a testament to the commitment to workplace safety.
As industries evolve, so does WHMIS, ensuring that the workforce remains not only compliant but also equipped to navigate the hazardous terrain of their specific workplaces. In the pursuit of a safer, healthier, and more secure working environment, WHMIS certification serves as a beacon, guiding industries through the intricacies of workplace safety.
By tailoring training, recognizing unique materials, ensuring regulatory compliance, considering industry-specific processes, planning for emergencies, integrating with broader training initiatives, and fostering symbol literacy, WHMIS certification stands as a testament to the commitment to workplace safety.
As industries evolve, so does WHMIS, ensuring that the workforce remains not only compliant but also equipped to navigate the hazardous terrain of their specific workplaces. In the pursuit of a safer, healthier, and more secure working environment, WHMIS certification serves as a beacon, guiding industries through the intricacies of workplace safety.
Level up your workplace safety!