Introduction
Workplace safety is integral to a thriving and successful workforce, and in Canada, the integration of the Workplace Hazardous Materials Information System (WHMIS) adds a layer of crucial protection. When it comes to creating a safety-conscious work environment, WHMIS plays a pivotal role in fostering a culture of safety across industries. From leadership commitment to safety success stories, each aspect contributes to building workplaces where safety is not just a practice but a shared value.
Importance of Comprehensive Safety Training
Comprehensive safety training is imperative in safe workplaces. Here’s why robust safety training programs are essential for fostering a culture of well-being in Canadian workplaces.
1. Risk Mitigation and Hazard Awareness
Comprehensive safety training is key to mitigating risks associated with hazardous materials in the workplace. For instance, in manufacturing, where employees handle various chemicals, training can educate workers on potential hazards, safe handling practices, and the importance of personal protective equipment (PPE). This raises hazard awareness, enabling employees to identify and address risks proactively.
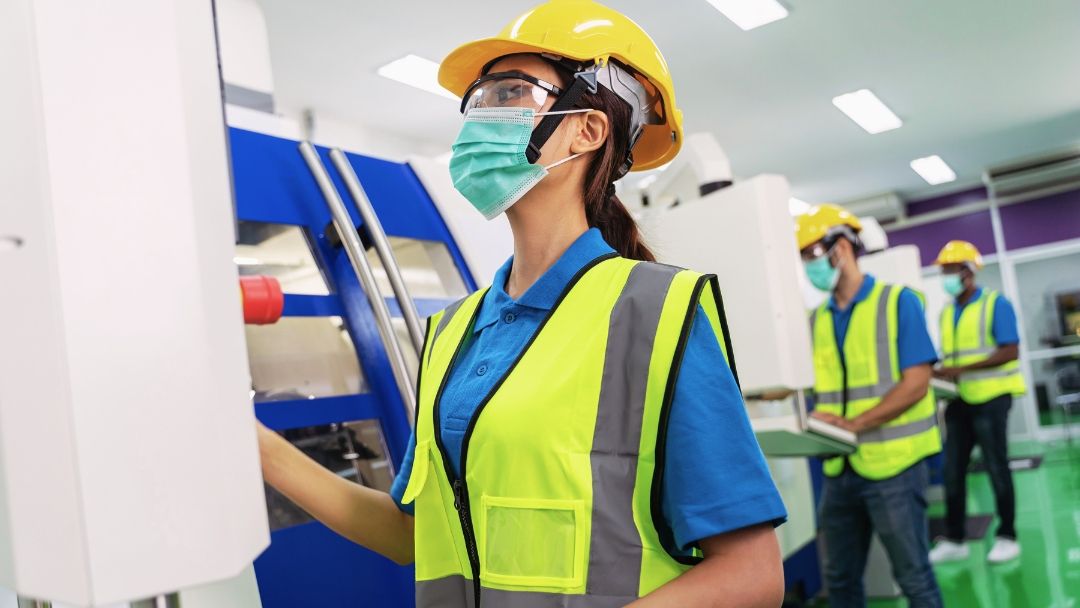
2. Compliance with WHMIS Regulations
A well-designed safety training program ensures compliance with WHMIS regulations in Canada. Employees need to understand WHMIS symbols, labels, and Safety Data Sheets (SDS) relevant to their work. Comprehensive training provides insights into WHMIS requirements, helping employees adhere to regulations and fostering a legally compliant workplace environment.
3. Emergency Response Preparedness
Training programs prepare employees for emergencies involving hazardous materials. In cases of spills or releases, workers need to know the appropriate response procedures. Realistic simulations and hands-on training help employees develop the necessary skills to respond effectively to incidents, minimizing potential harm and environmental impact.
4. Increased Employee Confidence and Engagement
Comprehensive safety training boosts employees' confidence in navigating workplace hazards. This confidence enhances their well-being and contributes to a more engaged workforce. For example, in construction, knowing how to handle and store materials safely can improve job satisfaction and overall safety.
5. Tailoring Training to Specific Work Environments
Each workplace has unique hazards, and comprehensive safety training allows for customization to specific environments. In a laboratory, employees may encounter different hazards than those in a warehouse. Tailoring training to workplace specific materials and processes ensures relevance and effectiveness.
6. Promoting a Culture of Responsibility
Comprehensive safety training instills a culture of responsibility among employees. In an industrial setting where chemicals are prevalent, employees who understand the potential risks and take responsibility for their safety contribute to a safer work environment. This culture extends to collaborative efforts in reporting hazards, ensuring a collective commitment to well-being.
7. Regular Updates on Changing Regulations
Safety training programs provide a way to keep employees updated on changing regulations, especially WHMIS. For instance, if there are updates to WHMIS symbols or labelling requirements, employees must be informed promptly. Regular training sessions offer opportunities to communicate these changes, keeping the workforce informed and compliant.
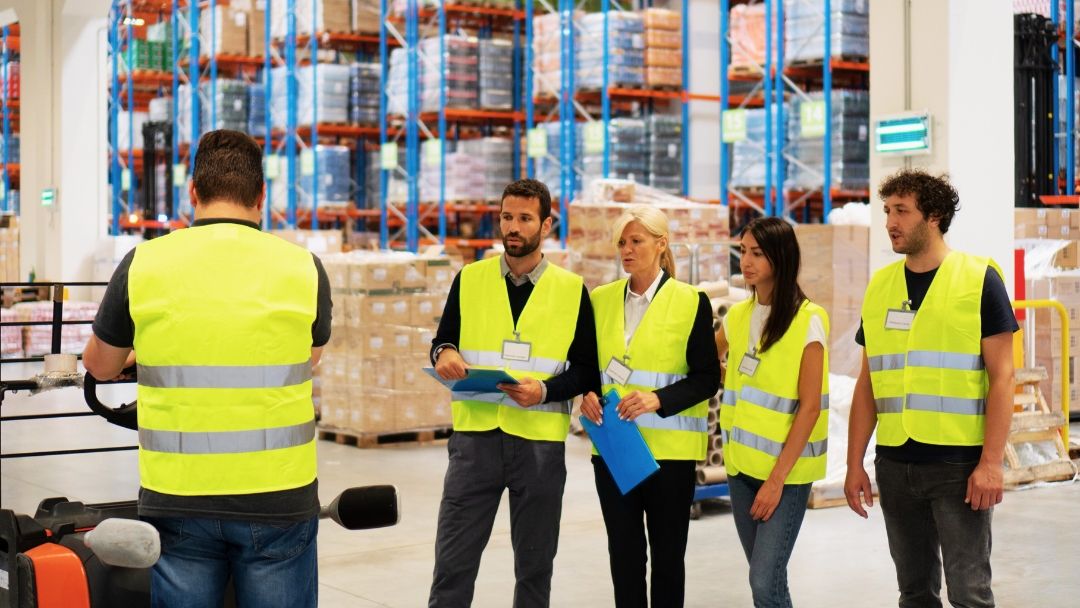
8. Demonstrating Organizational Commitment
A commitment to comprehensive safety training demonstrates the organization's dedication to employee well-being. This is crucial in high-risk industries such as chemical manufacturing or healthcare, where exposure to hazardous materials is common. Employees are more likely to embrace safety practices when they see their organization prioritizing health and safety.
The importance of comprehensive safety training in workplace safety and WHMIS certification extends beyond compliance. It is a proactive investment in risk mitigation, regulatory adherence, emergency preparedness, employee confidence, tailored training, a culture of responsibility, regulatory updates, and organizational commitment. As Canadian workplaces evolve, comprehensive safety training remains essential for creating environments prioritizing health and safety.
Designing Effective Training Programs
Creating effective training programs for your employees and supervisors is key to success in workplace safety and WHMIS certification. Here’s how to craft impactful training initiatives that significantly enhance WHMIS compliance and overall safety in Canadian workplaces.
1. Customization for Industry-Specific Needs
Designing effective training programs involves tailoring content to meet the specific needs of different industries. For example, in the healthcare sector, training may focus on the safe handling of pharmaceuticals and biohazardous materials, while in construction, emphasis may be placed on the proper use of construction chemicals. Customization ensures that training aligns with the unique hazards encountered in each industry.
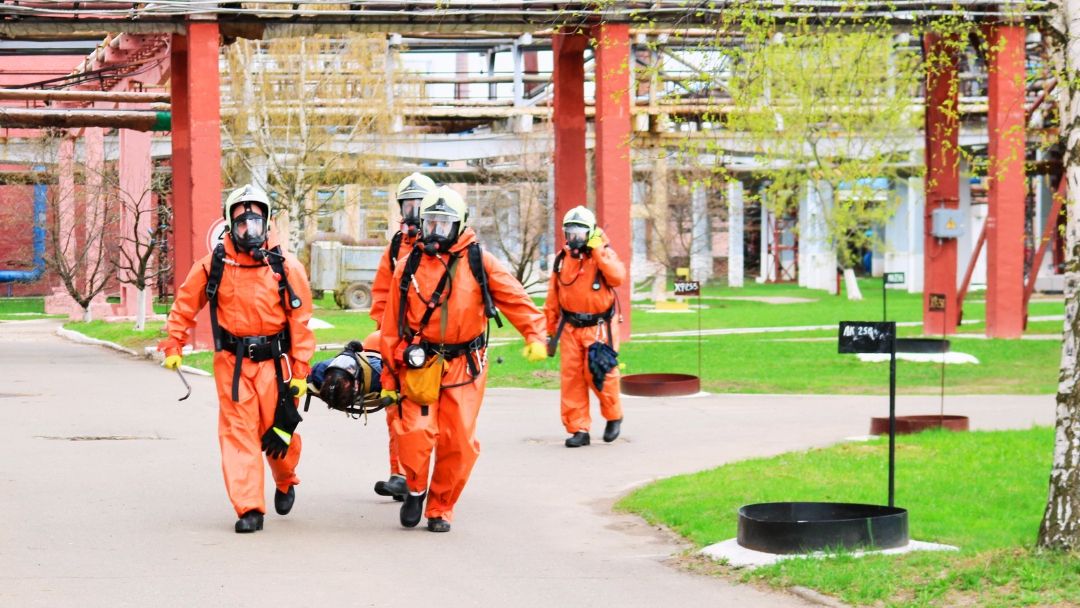
2. Interactive Learning Modules
Engagement is paramount in effective training programs. Incorporating interactive learning modules, such as online quizzes, scenario-based simulations, and hands-on exercises, enhances participant engagement. In a manufacturing setting, for instance, interactive modules could simulate real-life scenarios involving the handling of hazardous materials, allowing employees to apply theoretical knowledge in a practical context.
3. Realistic Simulations of WHMIS Scenarios
Simulating WHMIS scenarios within the training program provides practical insights for employees. For example, in a laboratory setting, a realistic simulation could involve identifying and responding to a spill of a hazardous chemical. These simulations prepare employees for actual workplace situations, ensuring that they can apply their knowledge effectively.
4. Clear Communication of WHMIS Symbols and Labels
Understanding WHMIS symbols and labels is crucial for workplace safety. An effective training program should focus on clear communication of these symbols. In a manufacturing facility, for instance, employees need to recognize and interpret symbols on containers to understand the hazards associated with the materials they are handling. Training programs should include practical exercises to reinforce symbol recognition.
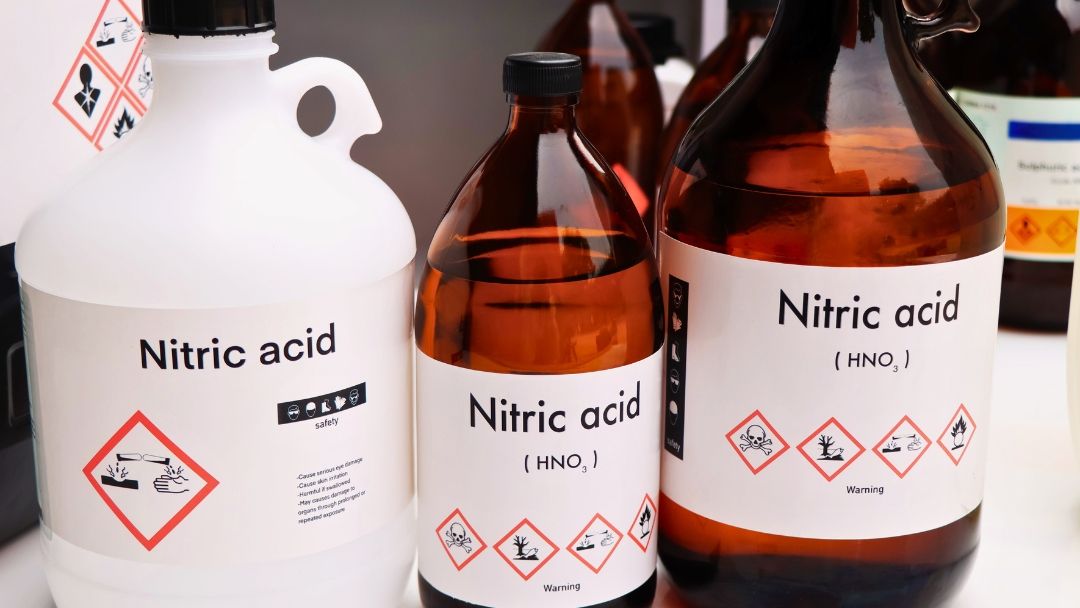
5. Accessible Online Platforms
The accessibility of training is vital, especially in diverse workplaces. Utilizing online platforms allows employees to access training materials at their convenience. In industries with shift-based schedules, such as healthcare or manufacturing, online platforms enable flexibility, ensuring that all employees can undergo training without disrupting operational workflows.
6. Integration with Workplace Procedures
Effective training programs seamlessly integrate with existing workplace procedures. For instance, in a warehouse setting, training should align with procedures for storing and handling materials. Integration ensures that employees understand how WHMIS principles fit into their daily routines, fostering practical application of knowledge.
7. Regular Assessments and Progress Tracking
Assessing employees' understanding and tracking their progress are integral components of effective training programs. Regular assessments, such as quizzes and tests, provide feedback on knowledge retention. In a logistics setting, for example, tracking progress ensures that employees handling hazardous materials during transportation are consistently updated on safety protocols.
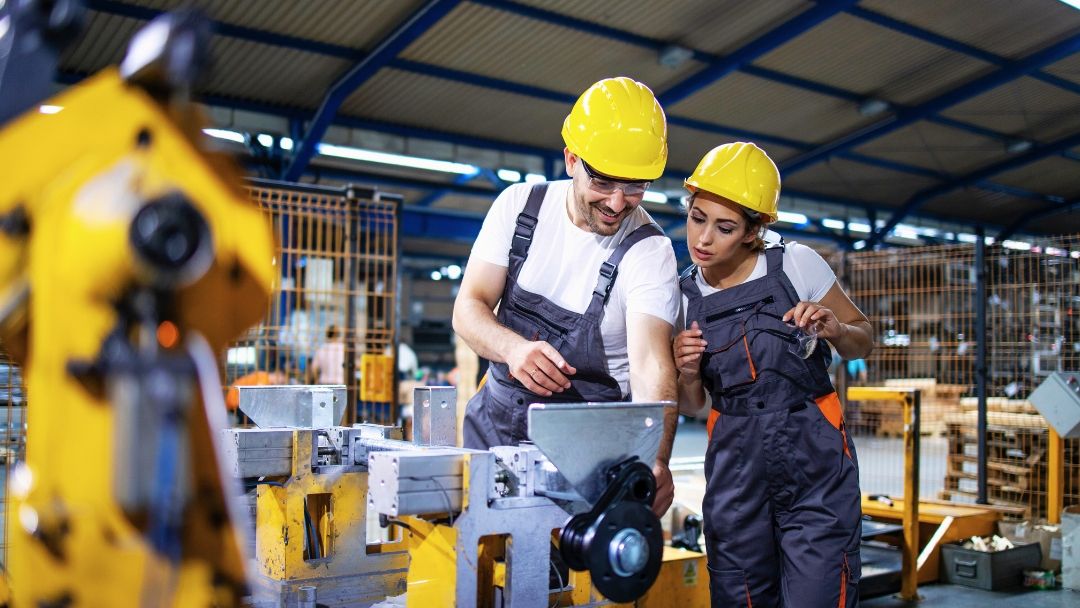
8. Feedback Mechanisms for Continuous Improvement
Establishing feedback mechanisms allows participants to provide insights into the effectiveness of the training program. In a laboratory environment, for instance, employees could offer feedback on the relevance of the training to their specific roles. Continuous improvement based on feedback ensures that the training program remains dynamic and responsive to evolving workplace needs.
In conclusion, designing effective training programs for WHMIS certification involves customization, interactive learning, realistic simulations, clear communication of symbols, accessibility, integration with procedures, regular assessments, and continuous improvement through feedback. These elements collectively contribute to a training blueprint that not only ensures WHMIS compliance but also empowers employees to navigate the complexities of workplace safety with confidence. As Canadian workplaces evolve, well-designed training programs serve as a catalyst for building a culture of safety and knowledge dissemination.
Implementing Ongoing Safety Education
The journey toward workplace safety and WHMIS certification extends beyond initial training, emphasizing the ongoing importance of safety education.
1. Regular Refresher Courses for WHMIS Certification Renewal
Implementing ongoing safety education involves scheduling regular refresher courses for WHMIS certification renewal. For instance, in a laboratory setting where employees handle hazardous chemicals, periodic refreshers ensure that knowledge about WHMIS symbols, labels, and updated regulations remains current. This proactive approach guarantees that employees consistently adhere to WHMIS standards.
2. Integration with Job-specific Training Programs
Ongoing safety education seamlessly integrates with job-specific training programs. In sectors like construction, where diverse materials are encountered, integrating WHMIS updates into job-specific training ensures that employees receive targeted information relevant to their roles. This integration enhances the applicability of WHMIS principles to real-world scenarios, fostering a holistic approach to workplace safety.
3. Awareness Campaigns and Information Dissemination
Promoting ongoing safety education involves conducting awareness campaigns and disseminating relevant information. In a manufacturing environment dealing with hazardous materials, regular communication channels, such as newsletters or digital displays, can convey updates on WHMIS regulations, safety tips, and success stories. This continuous flow of information keeps employees informed and engaged in maintaining a safe workplace.
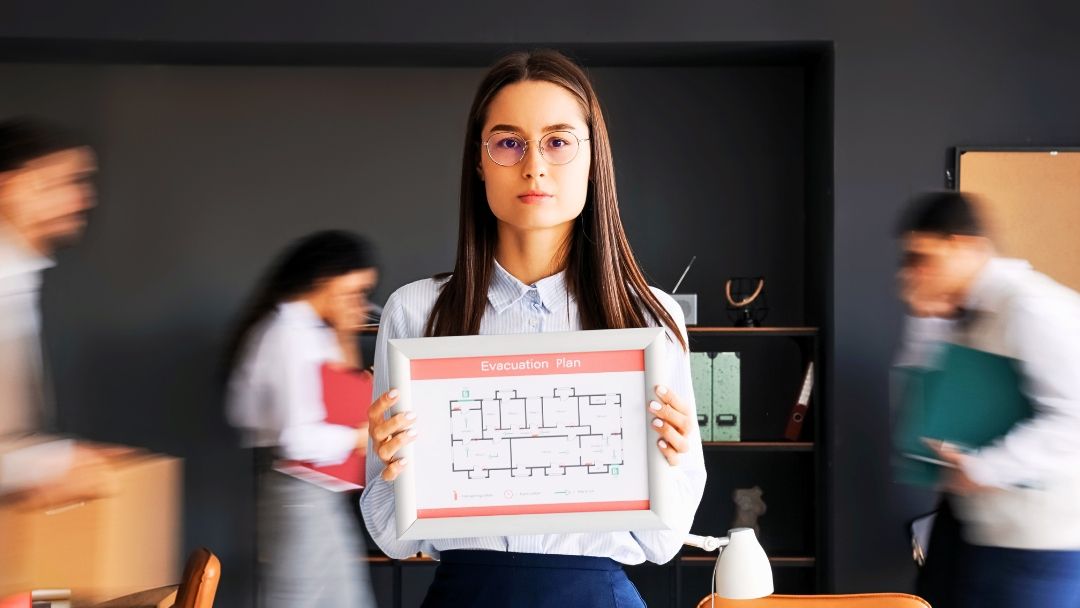
4. Incorporating WHMIS into New Employee Onboarding
Ensuring ongoing safety education includes incorporating WHMIS into new employee onboarding processes. In industries with high turnover rates, such as retail or hospitality, integrating WHMIS training into onboarding programs guarantees that every new employee receives foundational knowledge about hazardous materials from the outset. This proactive measure instills a safety-oriented mindset in employees from day one.
5. Practical Workshops and Hands-on Training Sessions
Ongoing safety education thrives on practicality, necessitating regular workshops and hands-on training sessions. In a warehouse setting, for instance, organizing sessions that simulate the proper handling and storage of hazardous materials reinforces theoretical knowledge. Hands-on experiences contribute to a deeper understanding and application of WHMIS principles in everyday work scenarios.
6. Utilizing Technology for Continuous Learning
Embracing technology plays a pivotal role in implementing ongoing safety education. For employees in the transportation sector, where handling hazardous materials during transit is common, leveraging digital platforms, webinars, and e-learning modules ensures continuous learning. Technology facilitates accessibility, allowing employees to stay updated on WHMIS requirements irrespective of their location or work schedule.
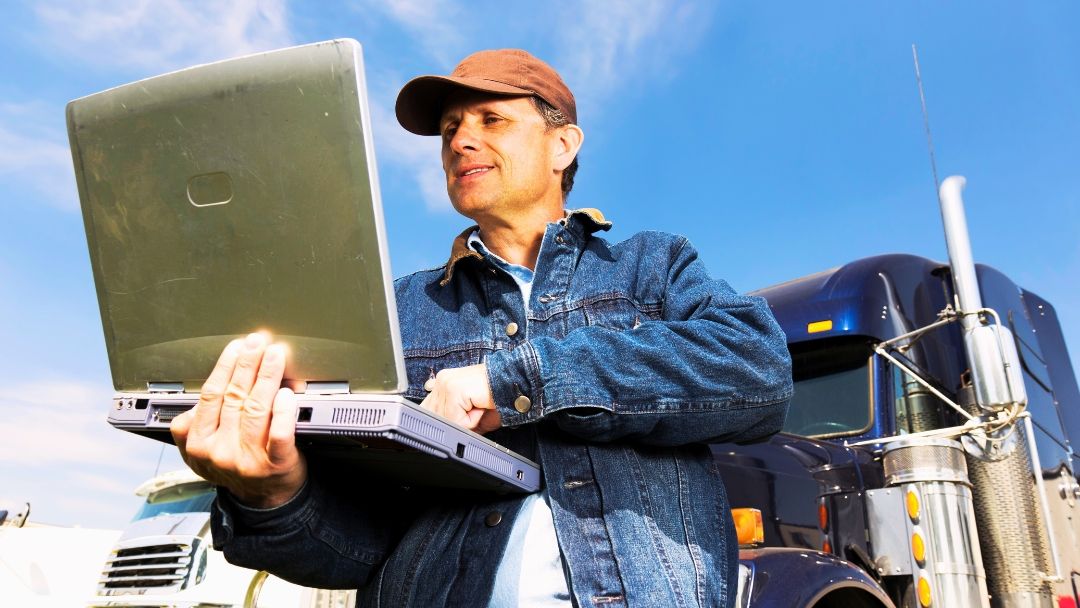
7. Establishing a Reporting and Feedback System
Implementing ongoing safety education involves establishing a robust reporting and feedback system. In healthcare, for example, where employees encounter various hazardous substances, having a system for reporting potential risks and providing feedback on safety protocols enhances continuous improvement. This two-way communication channel fosters a culture of vigilance and collaborative safety efforts.
8. Recognition and Rewards for WHMIS Compliance
Recognizing and rewarding WHMIS compliance motivates employees to actively engage in ongoing safety education. In a laboratory or research setting, where adherence to safety protocols is critical, acknowledging employees who consistently demonstrate WHMIS compliance creates positive reinforcement. Rewards may include certificates, commendations, or incentives, fostering a sense of achievement and commitment to safety
In essence, implementing ongoing safety education is a dynamic process encompassing refresher courses, integration with job-specific training, awareness campaigns, onboarding inclusion, practical workshops, technology utilization, feedback mechanisms, and recognition initiatives. This comprehensive approach not only sustains WHMIS awareness but also cultivates a workplace culture where safety is ingrained in every aspect of daily operations. As Canadian workplaces evolve, ongoing safety education stands as a cornerstone for adapting to changes in WHMIS regulations and fostering a resilient safety culture.
Creating a Safety-Conscious Work Environment
Ensuring a safety-conscious work environment is paramount to the well-being of employees and the overall success of Canadian workplaces.
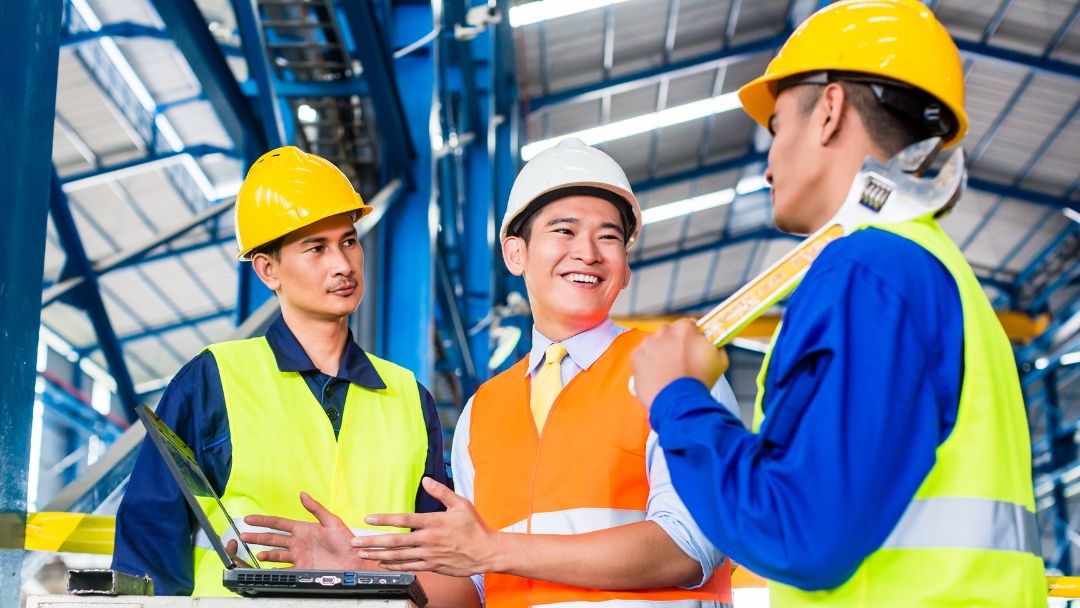
1. Leadership Commitment to Safety
Creating a safety-conscious work environment begins with strong leadership commitment. In construction, for example, where diverse hazards are present, leaders can demonstrate their commitment to safety by actively participating in WHMIS training alongside employees. This commitment sends a powerful message that safety is a shared responsibility at all levels of the organization.
2. Integration of WHMIS into Standard Operating Procedures
An essential aspect of a safety-conscious environment is the seamless integration of WHMIS into standard operating procedures. In manufacturing settings dealing with hazardous materials, incorporating WHMIS guidelines into daily procedures ensures that employees consistently follow safety protocols. This integration becomes ingrained in the work routine, promoting a culture where safety is not an afterthought but a fundamental part of every task.
3. Regular Safety Audits and Inspections
Maintaining a safety-conscious work environment involves conducting regular safety audits and inspections. In a laboratory setting, where precise adherence to safety measures is crucial, frequent inspections ensure that WHMIS standards are upheld. Identifying and addressing potential safety gaps proactively enhances the overall safety consciousness within the workplace.
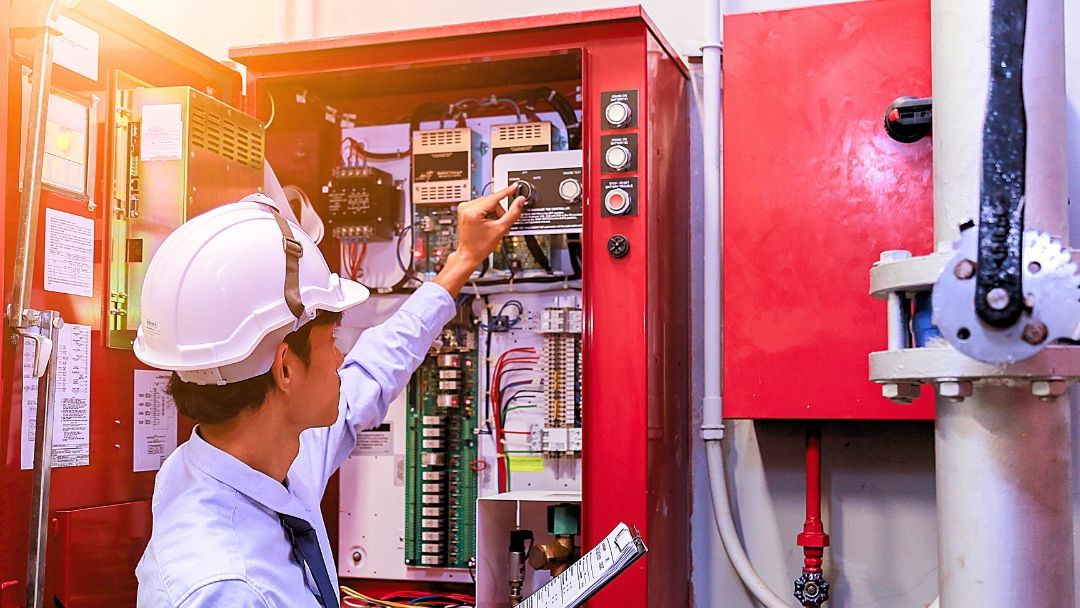
4. Employee Involvement in Safety Programs
Creating a safety-conscious culture relies on active employee involvement in safety programs. In a warehouse, for instance, where handling and storage of hazardous materials are common, empowering employees to actively contribute to WHMIS initiatives fosters a sense of ownership. Employee input in safety programs ensures that diverse perspectives are considered, enhancing the effectiveness of safety measures.
5. Communication of Safety Success Stories
Promoting a safety-conscious environment involves effective communication of safety success stories. In the healthcare sector, where exposure to hazardous substances is prevalent, sharing stories of successful WHMIS implementation and incident prevention highlights the positive impact of safety measures. These stories inspire employees and reinforce the importance of WHMIS compliance.
6. Training Beyond Compliance Requirements
Creating a safety-conscious work environment goes beyond meeting compliance requirements. In the automotive industry, for example, where various chemicals are used, providing additional WHMIS training beyond the mandatory requirements ensures a deeper understanding of hazards. This proactive approach equips employees with comprehensive knowledge, contributing to a heightened safety consciousness.
7. Establishment of Emergency Response Protocols
A safety-conscious environment necessitates the establishment of clear emergency response protocols. In industries like oil and gas, where the potential for emergencies exists, integrating WHMIS principles into emergency response plans ensures that employees are well-prepared to handle hazardous material incidents. Quick and efficient responses to emergencies are crucial for maintaining a safety-conscious culture.
8. Recognition for Safety Initiatives
Recognizing and acknowledging safety initiatives play a vital role in creating a safety-conscious work environment. In the manufacturing sector, for instance, where the handling of hazardous materials is routine, acknowledging teams or individuals for their commitment to WHMIS guidelines reinforces a culture where safety-conscious behavior is valued and celebrated.
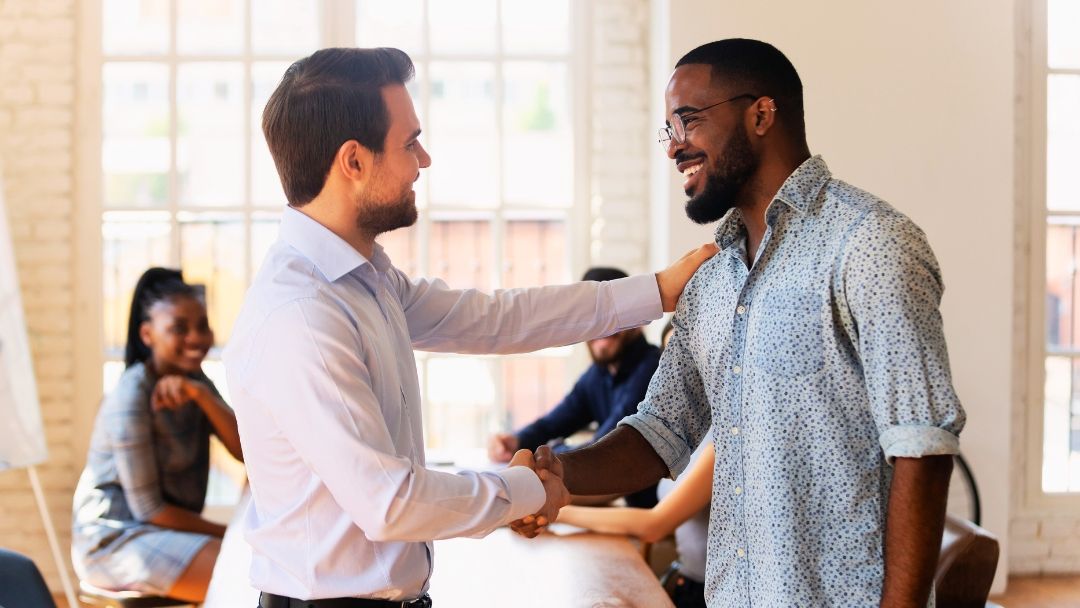
In conclusion, creating a safety-conscious work environment is a multifaceted endeavor that requires commitment, integration, involvement, communication, continuous training, emergency preparedness, and recognition. The pivotal role of WHMIS in fostering workplace safety cannot be overstated, as it provides the framework for understanding and mitigating the risks associated with hazardous materials. By embracing WHMIS as a foundational element, Canadian workplaces can cultivate a culture where safety is not just a priority but an integral part of their identity and success.
Conclusion
In the ever-evolving landscape of Canadian workplaces, the importance of prioritizing safety cannot be overstated. This blog has delved into the key elements of creating a safety-conscious environment, underscoring the integral role of WHMIS in this endeavor. By embracing WHMIS principles and weaving them into the fabric of daily operations, Canadian industries can build a culture where safety is not only a compliance requirement but a shared commitment. From leadership dedication to recognizing safety initiatives, every aspect contributes to a workplace where employees are not just protected from hazards but actively engaged in cultivating a secure and thriving professional environment.
Level up your workplace safety!